Aerospace PCB design is an intricate and specialized field addressing the extreme conditions of space and aviation. This exploration covers the selection of specialized materials, the rigorous process of component reliability and redundancy, and the unique challenges of outgassing, radiation, and mechanical stress. Each aspect plays a crucial role in ensuring the functionality and durability of PCBs in the demanding and dynamic aerospace environment.
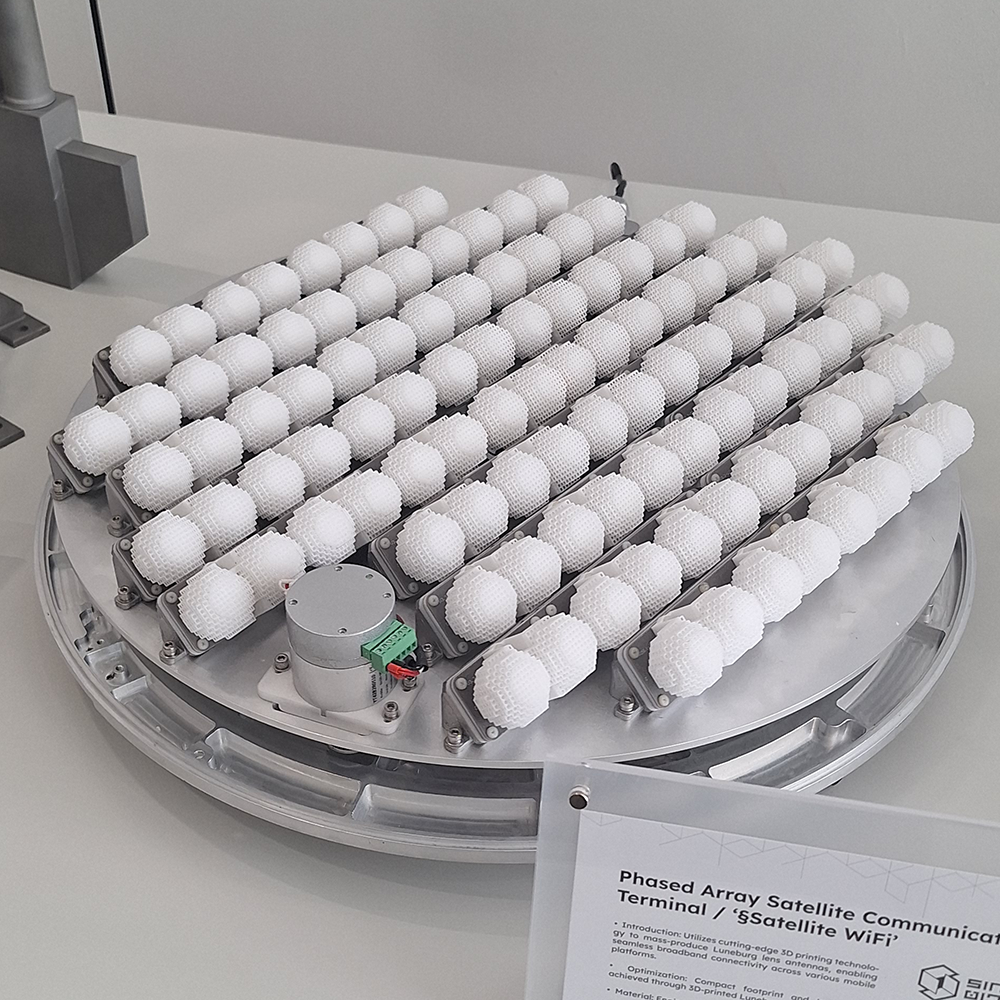
Advanced Material Selection and Design Standards
Aerospace PCBs begin with a fundamental choice of materials, far surpassing the capabilities of standard FR-4. Advanced composites like Polyimide, PTFE, or cyanate ester resins are selected for their unparalleled dielectric properties, thermal stability, and moisture resistance. These materials are critical for minimizing signal loss, especially in the high-frequency communication systems used in aerospace applications. They also offer enhanced durability under extreme environmental conditions, such as exposure to UV radiation, extreme temperatures, and vacuum conditions prevalent in space.
Thermal Management and Stability
Given the extreme temperature variations in aerospace environments, thermal management becomes a pivotal aspect of PCB design. Specialized materials with higher glass transition temperatures (Tg) are employed to maintain structural integrity and electrical performance. Additionally, designers implement advanced cooling techniques, including active and passive thermal management systems, to disperse heat effectively.
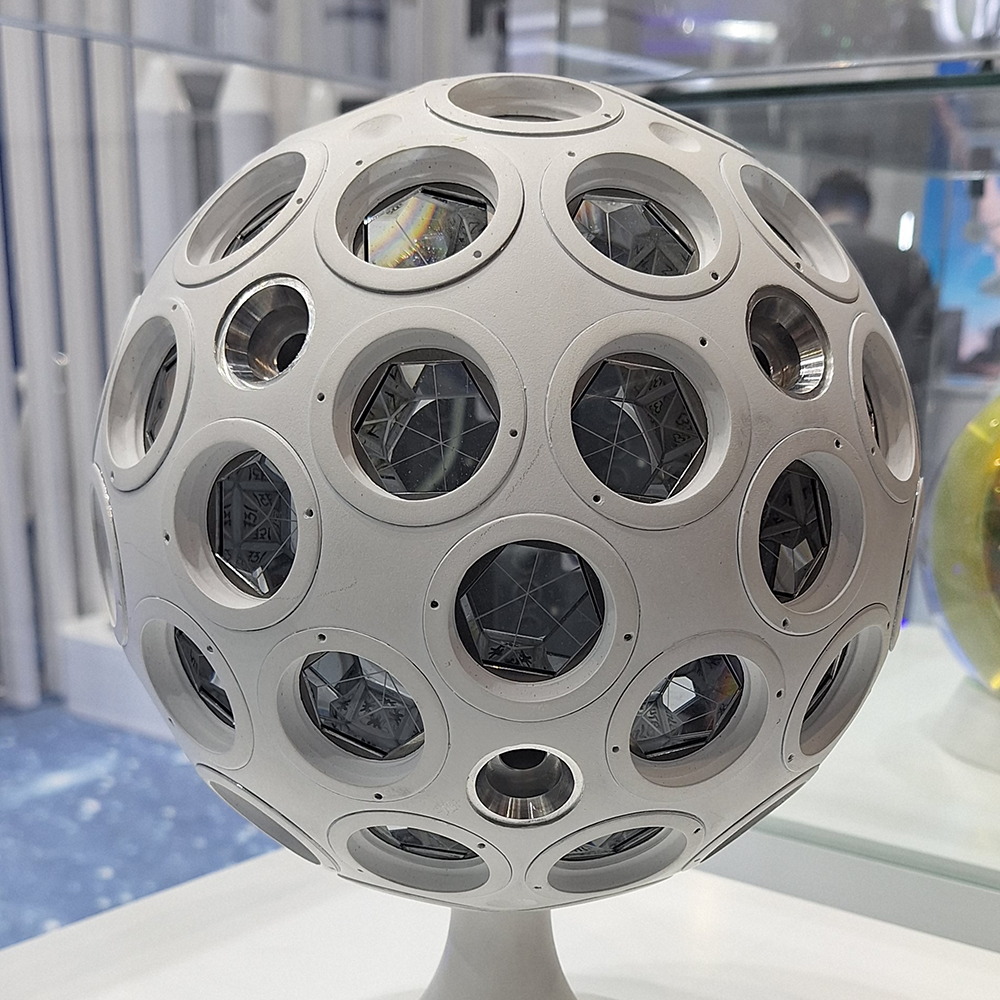
Component Selection, Reliability, and Redundancy
In aerospace PCBs, component selection is tightly regulated to ensure reliability. Adhering to military specifications like MIL-STD-202, components must withstand rigorous thermal, shock, and vibration tests. This ensures continuous operation in the dynamic and often harsh environment of aerospace applications.
Emphasizing Redundancy and Fail-Safe Design
A unique aspect of aerospace PCB design is the emphasis on redundancy. Critical systems incorporate duplicate or even triplicate subsystems to ensure continued operation in case of a component failure. This fail-safe design principle extends to various board functions, including power supply, data processing, and signal transmission. Designers often employ strategies like redundant power paths, dual processors, and multiple communication channels to ensure uninterrupted functionality.
Mitigating Outgassing, Radiation, and Mechanical Stress
Aerospace PCBs face unique challenges like outgassing in vacuum environments. Materials are meticulously chosen to align with NASA's ASTM E595 standards, ensuring minimal release of volatile compounds that might otherwise condense on optical instruments or sensitive surfaces.
Radiation Hardening and Shielding
Radiation hardening is another critical aspect. Components are specifically designed or selected to withstand the intense ionizing radiation encountered in space. Techniques like shielding with specific materials and circuit design modifications are employed to minimize the impact of radiation on PCB functionality.
High G-Force and Shock Endurance
Lastly, aerospace PCBs must endure significant mechanical stresses, including high G-forces and shocks, particularly during launch, re-entry, and in-flight maneuvers. The physical design, including component placement and board layout, is optimized to distribute these forces evenly. Enclosures and mountings are also designed to absorb and mitigate these forces, ensuring the structural and functional integrity of the PCB throughout its operational life.
Standards Reference
- IPC-6012 Class 3/3A: This standard relates to the performance specifications for high-reliability PCBs.
- MIL-STD-202: This is a military standard for electronic component testing, including environmental and durability tests.
- ASTM E595: This standard tests for total mass loss (TML) and collected volatile condensable materials (CVCM) from outgassing in a vacuum environment.
- MIL-STD-810: This standard covers environmental engineering considerations and laboratory tests for military systems and equipment.
- NASA Outgassing Database: This database lists materials that have been tested and meet NASA's outgassing criteria.
- ECSS-Q-ST-70-12C: European Cooperation for Space Standardization, This standard specifies the requirements for the supplier and PCB manufacturer for PCB design.